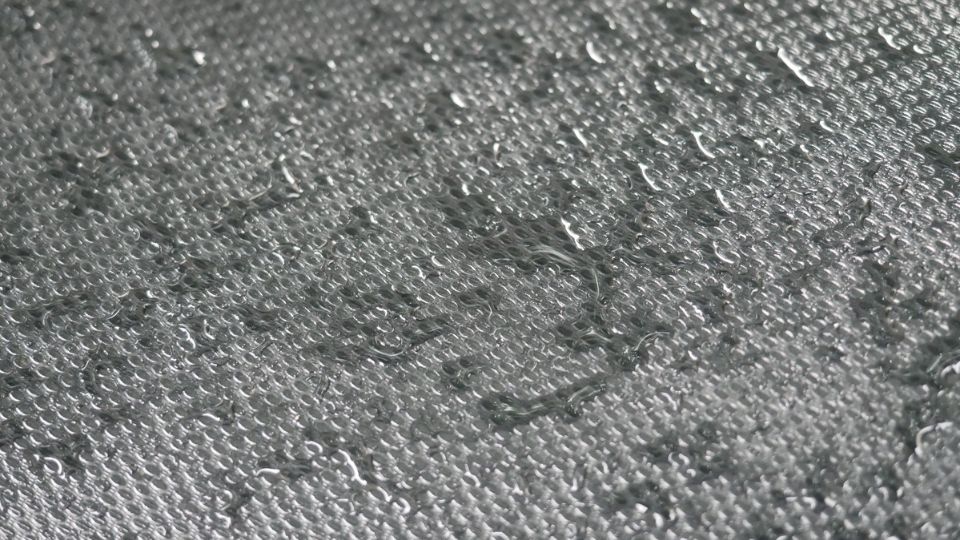
Le premesse
Uno dei problemi principali dei materiali compositi come quelli in fibra di vetro (GFRP) e fibra di carbonio (CFRP), molto utilizzati in aeronautica, ma non solo, è la loro capacità di assorbire umidità che ne pregiudica la resistenza e la rigidezza. L’umidità, infatti, può penetrare nel materiale attraverso piccoli difetti nella vernice, microfessure o punti di connessione, compromettendone l’integrità nel tempo.
Eventi storici hanno mostrato quanto questo aspetto possa essere anche molto critico. Nel 2015, un Airbus A310 Polaris fu coinvolto in un incidente legato a un effetto combinato tra umidità e alte temperature, amplificate dalla vernice scura del composito. Anche il celebre Concorde, nel 1989, subì un grave incidente dovuto alla delaminazione tra gli strati del materiale composito, dove l’umidità aveva compromesso lo strato adesivo che teneva insieme le parti.
Episodi che dimostrano che il tema dell’assorbimento di umidità nei materiali compositi non è un argomento secondario. È, invece, una questione ancora oggi fondamentale per garantire la sicurezza e la longevità delle strutture, soprattutto in ambito aeronautico.
Cosa succede quando un materiale composito assorbe umidità?
L’umidità agisce come un vero e proprio “plasticizzante”: altera le proprietà meccaniche del materiale, rendendolo meno resistente. Nei polimeri, ad esempio, può interferire con i legami molecolari, indebolendoli o addirittura rompendoli in modo irreversibile.
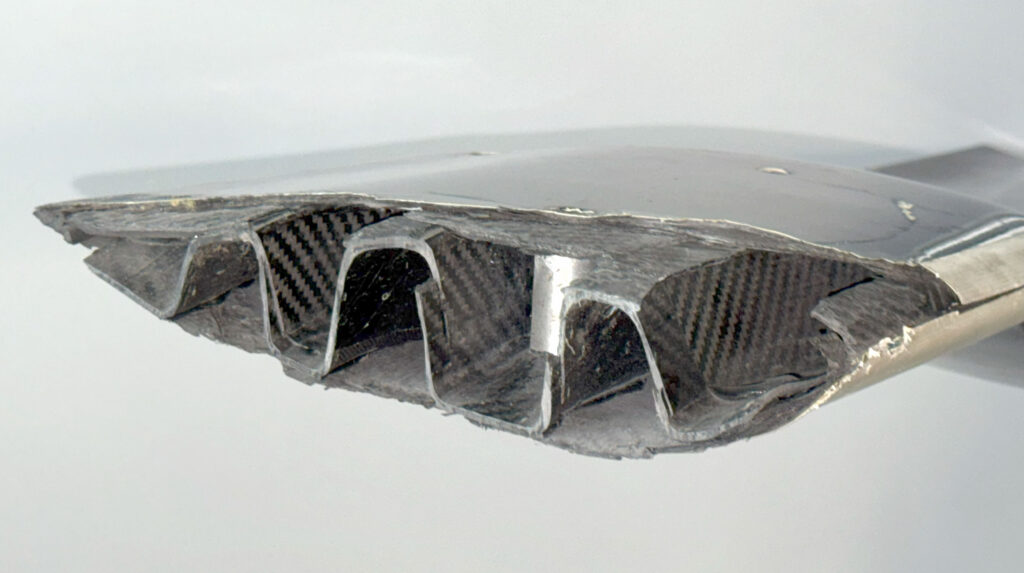
I danni da assorbimento di umidità più comuni sono:
- delaminazione, cioè il distacco tra gli strati del materiale;
- formazione di cricche all’interno del materiale chiamate cricche intralaminari, sono danni, crepe che si formano all’interno del materiale e dunque non visibili esternamente;
- scarsa adesione tra le fibre di rinforzo e la matrice, con conseguente peggioramento della capacità di sostenere il carico.
Gli esperimenti di laboratorio confermano questa tendenza. Campioni di compositi GFRP e CFRP sottoposti a condizioni di umidità e alte temperature hanno mostrato un netto peggioramento delle proprietà rispetto a campioni mantenuti in condizioni asciutte. Questi risultati mettono in evidenza quanto sia importante studiare il fenomeno e sviluppare soluzioni che riducano l’impatto dell’umidità sulle strutture.
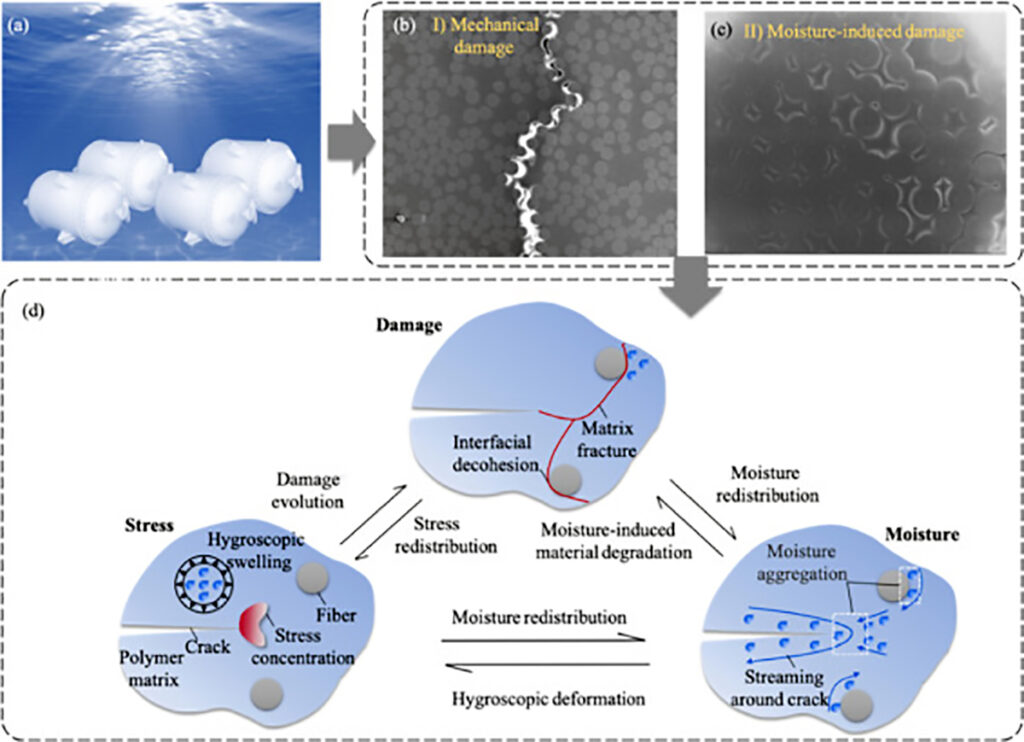
La nuova frontiera del monitoraggio: i sensori FBG
Negli ultimi anni, la tecnologia ha fatto passi da gigante nel monitorare e prevenire i danni causati dall’umidità e da altri fattori. Tra le soluzioni più innovative spiccano i sensori a reticolo di Bragg in fibra ottica (FBG), che possono essere integrati direttamente nei materiali compositi per monitorare in tempo reale lo stato di salute della struttura.
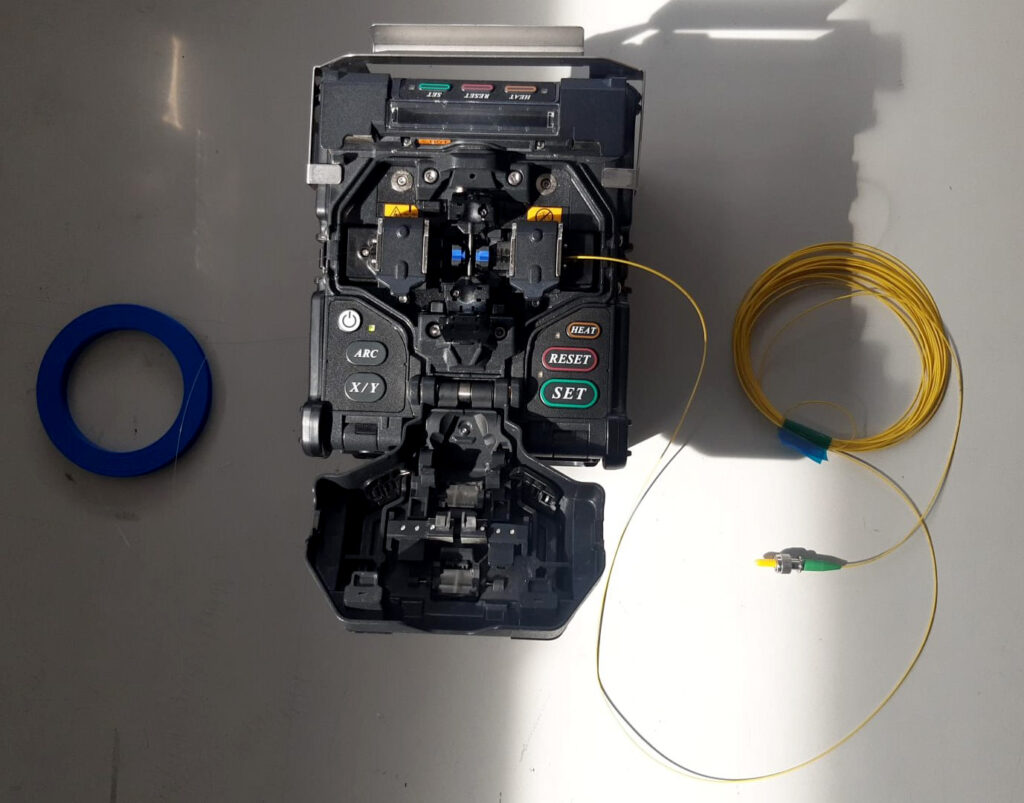
Questi sensori sono in grado di rilevare variazioni legate a sollecitazioni, umidità o danni, fornendo informazioni preziose. I progressi principali in questo campo includono:
- la miniaturizzazione delle fibre ottiche e dei componenti, rendendoli sempre più compatti e resistenti;
- tecniche avanzate di iscrizione dei sensori per migliorare la qualità del segnale;
- sistemi robusti, progettati per funzionare anche in condizioni operative estreme, come alte temperature o vibrazioni intense.
L’innovazione del sensore brevettato
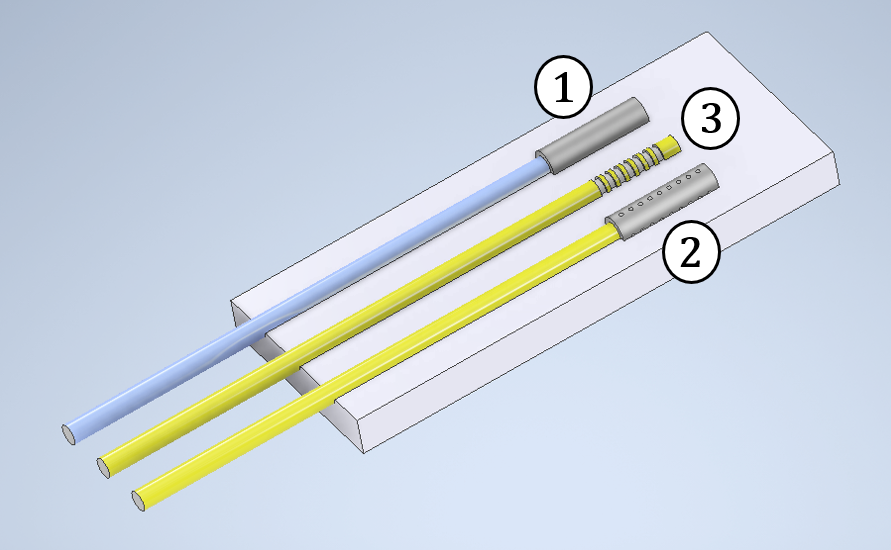
Anche i sensori in fibra ottica presentano problematiche legate all’assorbimento di umidità da parte del loro rivestimento polimerico. Tale assorbimento può introdurre errori nella misura, falsando la rilevazione di carichi termici e/o meccanici.
Per risolvere questo problema, il gruppo di ricerca ha avuto un’idea innovativa: trasformare quello che era un limite in una soluzione.
I ricercatori hanno pensato di sfruttare l’igroscopicità del rivestimento per misurare l’umidità assorbita dal componente. Questo approccio ha portato alla creazione di un nuovo sensore brevettato, capace attraverso l’uso di tre sensori FBG di misurare e disaccoppiare le dilatazioni termiche, le deformazioni meccaniche e quelle dovute all’assorbimento di umidità.
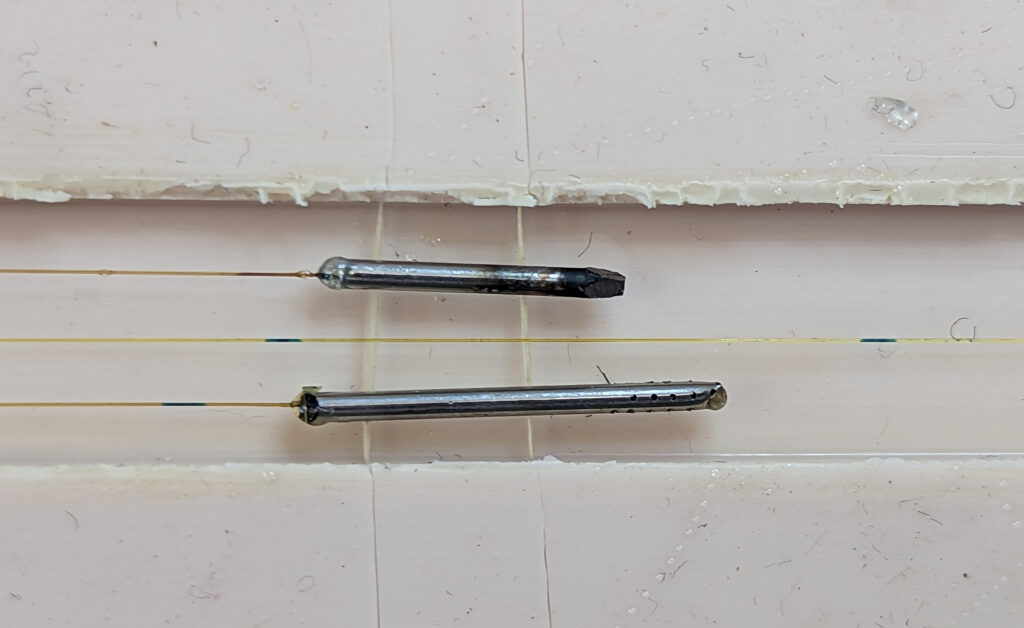
Le applicazioni
Il nuovo sensore brevettato non solo rileva la quantità di umidità assorbita dal componente, ma fornisce anche dati fondamentali per stimare il degrado delle proprietà meccaniche della struttura, permettendo una diagnosi accurata e una prognosi sulla sua vita operativa residua. Questo innovativo sistema di monitoraggio trova applicazione in una vasta gamma di settori, tra cui:
- aeronautica e elicotteristica;
- nautica e imbarcazioni;
- pale eoliche off-shore.
Ovunque vi siano strutture in materiale composito soggette a condizioni ambientali umide, il sensore può contribuire a migliorare la sicurezza e la durabilità delle infrastrutture.
Grazie a questa tecnologia, è possibile innalzare il livello di affidabilità delle strutture del futuro, segnando un passo avanti nell’innovazione e nella protezione delle infrastrutture critiche.
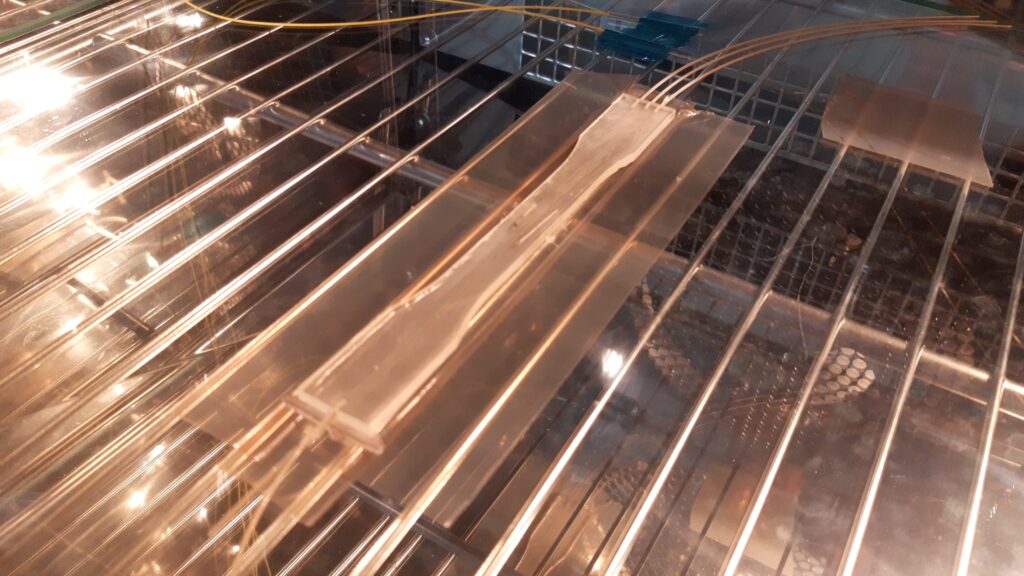
Il team di ricerca
Il team che ha svolto la ricerca è composto dai Professori Giuseppe Sala e Pietro Aceti, del Dipartimento di scienze e tecnologie aerospaziali (DAER) del Politecnico.

Prospettive future
Il sensore brevettato apre nuove prospettive scientifiche nello studio dei materiali compositi, permettendo lo sviluppo di modelli più precisi sugli effetti dell’umidità e favorendo ricerche su rivestimenti intelligenti e sensori multifunzionali. I dati raccolti potranno guidare la standardizzazione internazionale e stimolare collaborazioni interdisciplinari per migliorare la sicurezza e la durabilità delle strutture.